23–24 октября 2019 г. в Москве состоялся первый отраслевой форум «Информационные технологии в металлургии и металлообработке». На нем обсуждались основные тенденции развития ИТ в металлургии и металлообработке в России и за рубежом, а также возможности применения в металлургии таких технологий, как большие данные, управление полным жизненным циклом изделий и оборудования, предиктивной аналитики, решения индустриального Интернета вещей, отраслевые особенности исполнения Закона № 187-ФЗ «О безопасности КИИ». Партнерами форума стали компании NetApp, Veeam, «АМТ-ГРУП» и «АйТи Бастион». В форуме приняли участие представители Казахстана, Белоруссии и Азербайджана. За два дня мероприятие посетили 134 специалиста из металлургической, металлообрабатывающей и горнодобывающей промышленности, представители вузов и регуляторов. Организатором форума выступил Издательский дом «Коннект».
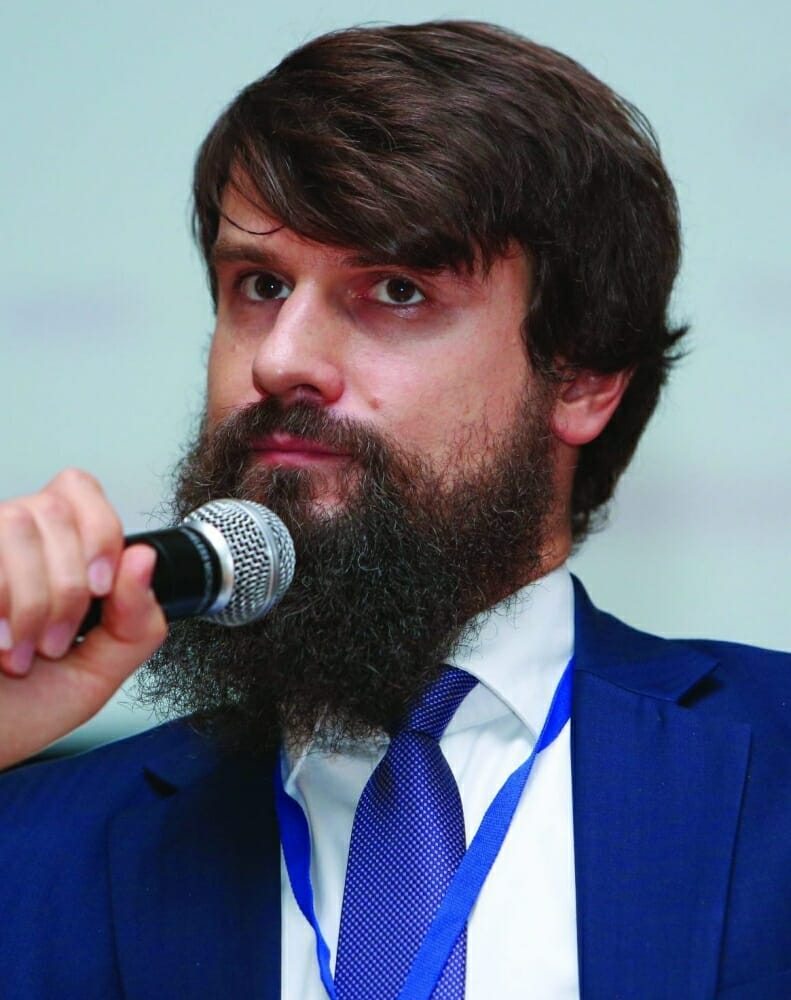
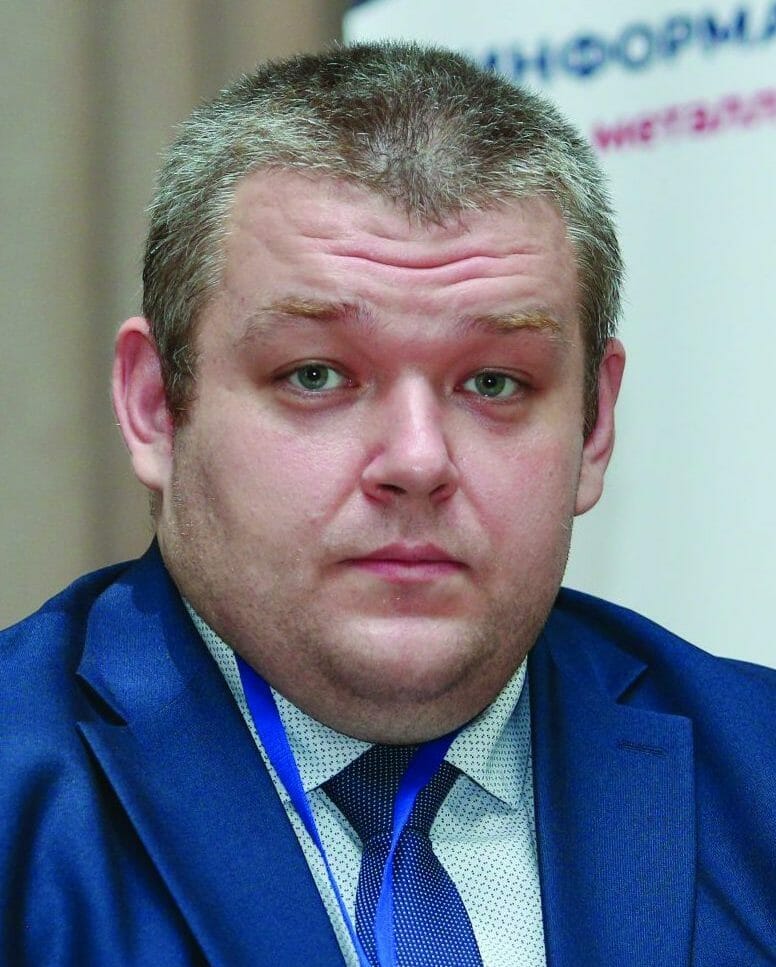
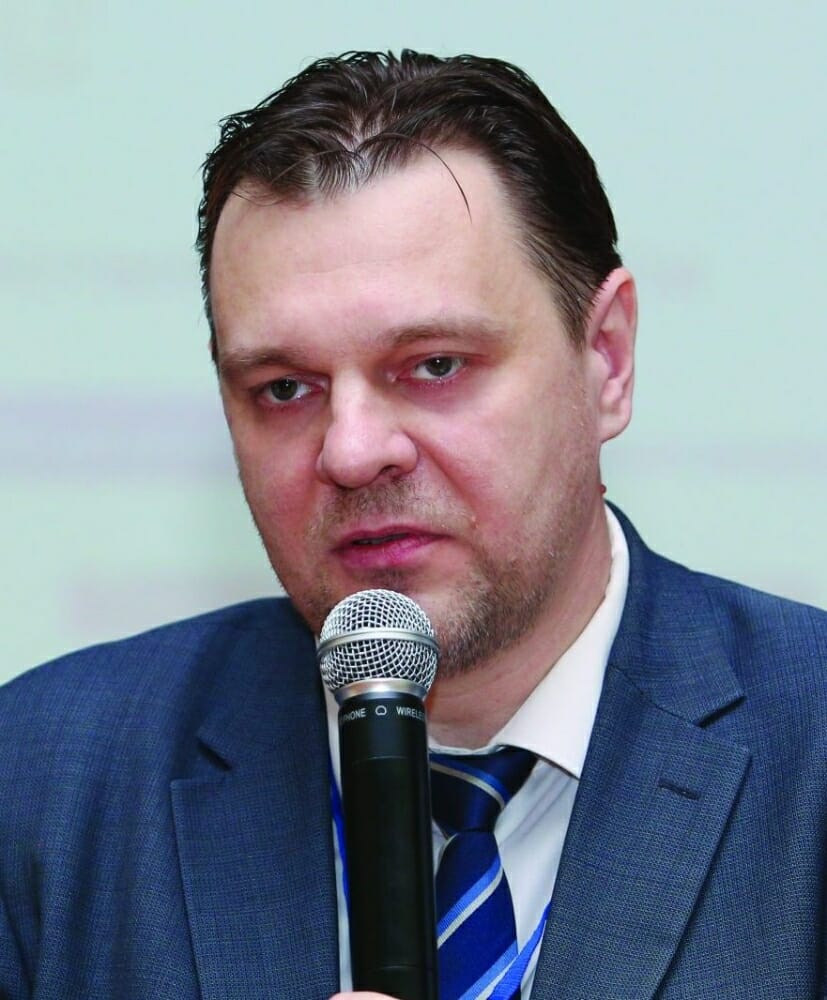
Начался форум с дискуссии, в которой обсуждались общие вопросы цифровизации в металлургии. Собравшиеся отметили, что цифровизация предприятий металлургической отрасли хотя и уступает финансовой сфере и телекоммуникационной отрасли, все-таки соответствует насущным потребностям металлургических и металлообрабатывающих предприятий. Ренат Назыров, директор департамента «Сквозная автоматизация» Объединенной компании РУСАЛ пояснил, что «в металлургические компании пришли CDO в первую очередь из банковского сектора». Именно специалисты из финансового сектора и телекома сейчас и являются основными источниками инновационной деятельности.
«Цель цифровизации – догнать не банки или телеком, а наших ближайших конкурентов», – отметил Сергей Тимашов, директор департамента информационных систем ООО «УК Мечел-Сталь». Действительно, металлургическая отрасль России конкурирует в основном не внутри страны, а в большей степени за ее пределами, где цифровизация уже идет полным ходом. Чтобы не отстать от своих западных конкурентов, российские металлургические компании вынуждены использовать цифровые сервисы и другие элементы стратегии «Производство 4.0». Но, по словам Рената Назырова, в ИТ-отделах не требуется много людей – они лишь обеспечивают функционирование инфраструктуры. В первую очередь необходимо обучить производственный персонал применению ИТ в повседневной работе. Однако технологи и другие производственные специалисты не торопятся осваивать информационные технологии, потому именно для их убеждения зачастую и нужны специалисты по цифровизации. «Цифровой сотрудник» – один из компонентов «Индустрии 4.0».
Хотя некоторые участники дискуссии и признались, что считают цифровизацию рекламным трюком западных компаний, автоматизация технологических процессов на промышленных предприятиях проводится достаточно давно с использованием различных технологий и продуктов. Поэтому, по мнению Андрея Сорокина, директора дирекции информационных технологий ПАО «Трубная металлургическая компания», основными драйверами цифровизации в металлургической промышленности будут унификация оборудования и построение единых цифровых сервисов. Заинтересованность в разработке новых цифровых сервисов на базе существующих систем контроля, автоматизации производства и деятельности предприятия высказали практически все участники панельной дискуссии.
Металлургическая автоматизация
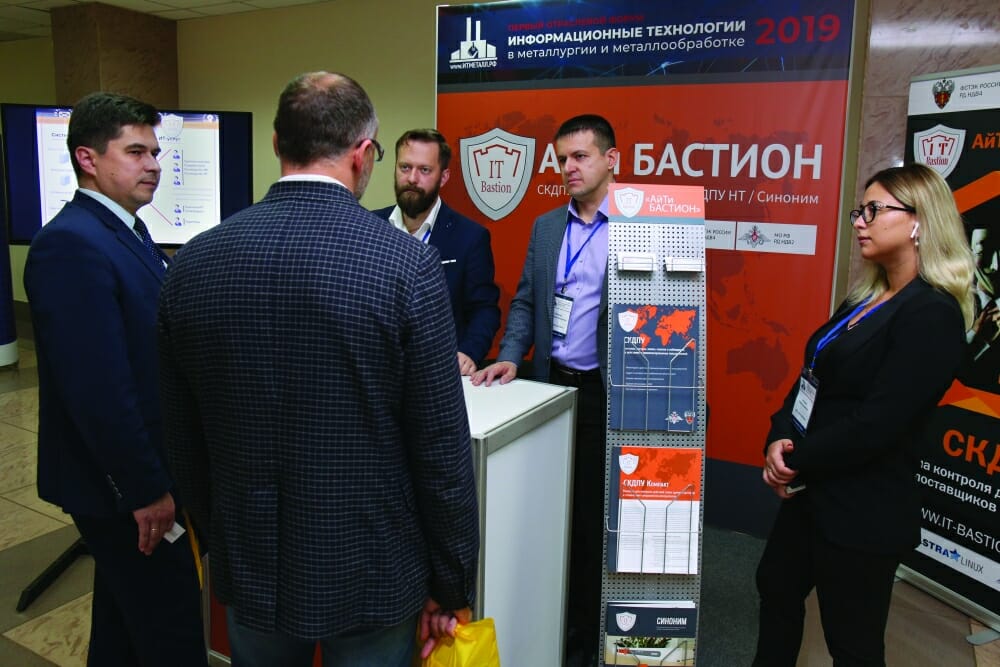
Сессия «Классические вопросы информатизации в металлургии» была посвящена внедрению различных систем: MES, ERP, ЭДО, системы управления качеством продукции и интеграционной шины. Больше всего внимание слушателей привлекли доклады Рената Назырова, который рассмотрел современные требования, предъявляемые к MES металлургическими предприятиями, и Антона Омигова, менеджера группы «Документооборот» отдела корпоративных разработок ООО «ММК-Информсервис», который рассказал о разработке собственной системы электронного документооборота, ориентированного на работу в металлургической отрасли. Эти доклады были признаны одними из лучших по результатам голосования слушателей.
Ренат Назыров отметил, что сейчас само по себе наличие MES уже не является конкурентным преимуществом. Идеология автоматизации управления производством развивалась в течение прошедших 20 лет, и практически все компании уже внедрили те или иные варианты MES. Однако наличие MES, которая позволяет координировать действия всех остальных элементов автоматизации производства, обеспечивает возможность оптимизации технологического процесса. Современные MES сокращают трудозатраты на планирование производства до 7%, потребление энергоресурсов – на 10, на ремонт и техническое обслуживание – до 15, на формирование отчетности – до 35%, а также дают возможность снизить складские запасы материалов на 3% и произведенной продукции на 25%. Кроме того, повышается контроль качества производимой продукции – на 5% уменьшается количество несоответствующей продукции. Этих показателей удается достигнуть за счет обмена информацией между корпоративными информационными системами через MES и более точного планирования выполняемых операций.
В цифровизации современных предприятий важную роль играет применение сотрудниками цифровых средств общения, взаимодействия и принятия решений. О создании среды электронного взаимодействия рассказал в своем докладе Антон Омигов, который занимался разработкой системы электронного документооборота для группы компаний ПАО «ММК». Ранее для организации документооборота использовали Lotus Notes, затем был внедрен Domino с мобильными приложениями, но пользоваться этими иностранными разработками оказалось довольно сложно. В компании было принято решение самостоятельно разработать удобный и мобильный документооборот, который позволил бы обмениваться информацией в единой инфраструктуре предприятия. Так было создано приложение под названием «Атач», которое по сути представляет собой классическую систему документооборота. Система оказалась настолько удобной, что теперь все высшее руководство 44 компаний, входящих в холдинг, активно его использует, а компания ООО «ММК-Информсервис» сейчас готовит коммерческий выпуск разработанного продукта.
Аналогичный пример внедрения на промышленном предприятии среды единого взаимодействия привел в своем докладе Игорь Гусенков, заместитель генерального директора по корпоративным коммуникациям АО «Загорский Трубный Завод». Он рассказал о внедрении на своем предприятии внутренней социальной сети для стимулирования прямого взаимодействия между сотрудниками. Оказалось, что созданная специалистами внутрикорпоративная социальная сеть на базе «Битрикс 24» и получившая название Vtrube позволила сотрудникам компании быстрее взаимодействовать с коллегами и тем самым оперативно решать все вопросы. К тому же социальная сеть интегрирована с общей производственной системой завода, что дает возможность публиковать в ней сведения о текущем состоянии производства, выполненных заданиях и качестве производимой продукции.
В работе секции при помощи удаленного подключения по Skype приняла участие Анастасия Никитина, финансовый директор АО «Металлургический завод «Петросталь», которая рассказала об опыте внедрения на своем заводе «1С:Предприятие 8. ERP Управление предприятием 2». Предприятие, не нанимая специалистов-интеграторов, силами трех собственных программистов смогло в течение 3,5 лет внедрить «из коробки» единую систему финансового учета, контроль производства и финансовый контроль. В 2018 г. завод полностью перешел на новую производственную систему российского разработчика.
Евгений Зайцев, директор по информационным технологиям, АО «Загорский Трубный Завод» — о внедрении интеграционной шины на российской платформе SIS. Шина позволяет интегрировать самые разнообразные информационные системы. На ЗТЗ она позволяет обмениваться информацией между SAP, 1C, АСУ ТП TraceMod, системой транспортной логистики АСУ ТЛ, QlikSense и даже «Битрикс», на основе которого построена социальная сеть предприятия. В результате, именно интеграционная шина и стала основой той самой координирующей системой, о которой говорил Ренат Назыров.
Павел Исаев, начальник бюро службы автоматики АО «Волжский трубный завод», – о проекте по управлению качеством в режиме реального времени. Он был инициирован в 2019 г., чтобы с помощью информации от датчиков, установленных на производственном оборудовании, можно было в режиме реального времени обнаруживать некорректную работу агрегатов и вовремя их перенастраивать. Когда обнаружение дефектов выполнялось с помощью выходного контроля, до 40% труб оказывалось забракованными. Сейчас количество брака удалось сократить на 30%, поскольку обнаружение дефектов производится в том числе и на промежуточных этапах.
Также в этой сессии Аркадий Козлов, руководитель проекта по автоматизации АО «Чепецкий механический завод», рассказал о внедрении MES-системы Hydra на созданном с нуля производстве сверхпроводников – внедрение указанной MES было требованием заказчика, чтобы он мог отследить качество производимой продукции. В результате прокатные станы полностью оснащены контролирующим оборудованием, что позволяет оценивать качество производимой продукции в режиме реального времени и передавать сведения о нем заказчику – без документов по качеству не выполняется отгрузка готовой продукции. Таким образом, заказчик вовлечен в работу предприятия, как это и предполагает концепция «Индустрии 4.0».
Передовые разработки
Вопросы использования искусственного интеллекта на производстве обсуждались в сессии «Искусственный интеллект в металлургии». Здесь были представлены доклады по использованию технологий машинного зрения для выявления нарушений в технологических процессах или правил промышленной безопасности, анализу данных с датчиков для обнаружения брака и дефектов, а также были рассмотрены рекомендации по точному подбору химического состава плавки с помощью анализа исторических данных.
Опытом промышленного использования искусственного интеллекта поделился Олег Карташев, технический архитектор ОАО «Северсталь-Инфоком». Правда, речь в его докладе шла в основном о применении компьютерного зрения, которое используется на предприятиях группы «Северсталь» уже достаточно активно, практически на всех переделах: при добыче угля и руды, производстве стали и изделий из нее, дистрибуции продукции, обеспечении промышленной безопасности, в обслуживании и ремонтах и даже в документообороте. Основными направлениями являются контроль соблюдения технологии, позиционирование и выравнивание объектов, обнаружение опасных объектов на производстве, контроль материалов и их потоков, инспекция поверхностей, выявление скрытых и неразличимых отклонений, техническое зрение транспортных роботов, соблюдение техники безопасности и др. Причем для каждого применения уже есть, как минимум, работающие прототипы.
Аналогичные разработки по использованию механизмов искусственного интеллекта в производстве ведутся и на других металлургических предприятиях. Например, на ПАО «ЧТПЗ» была разработана программа «Помощник сталевара», которая позволила ускорить процесс получения точного химического состава плавки в агрегате «ковш-печь», минимизировав количество химических проб. О разработке такого инструмента рассказал на конференции Михаил Ильиных, инженер ПАО «ЧТПЗ». Приложение по косвенным измерениям, таким как температура плавки, ее масса, окисленность и др., предсказывает химический состав плавки и рекомендует добавить те или иные корректирующие ферро-материалы. Посредством данного приложения удалось сократить количество корректирующих материалов и таким образом экономить на дорогостоящих присадках.
Подобный проект по предсказанию качества трубной продукции по характеристикам технологического процесса был реализован на АО «Загорский Трубный Завод» компанией Conundrum на базе одноименной платформы для промышленного использования искусственного интеллекта. Компании, по словам Виктора Портнова, директора по продукту ООО «Конандрум», удалось построить систему, которая по показаниям с различных датчиков может определить, на каком из шести переделов, существующих на заводе, были допущены отклонения от нормального технологического процесса. Причем сроки получения данных достаточно короткие, что позволяет не завершать процесс формирования трубы, если на ранних этапах ее изготовления были допущены существенные отклонения от нормы. При этом решение, анализируя поступающую с датчиков информацию на большом количестве наблюдений, дает возможность подобрать положительные шаблоны оптимизации и поддержания технологических настроек, предоставляя их технологам в качестве рекомендаций по оптимизации процесса. Если на каком-то переделе система фиксирует отклонение от нормального поведения оборудования, процесс можно оперативно остановить и настроить оборудование, чтобы не допустить брака по большому количеству изделий.
Ильнур Фархутдинов, заместитель главного конструктора инновационных автомобилей Научно-технического центра ПАО «КамАЗ», рассказал о проекте автономного автомобиля для движения на закрытых и полузакрытых территориях. Для этого подготовлен КамАЗ-43083, который будет автоматизировать внутризаводскую логистику. Вначале на его примере компания отработает алгоритмы автономного вождения на собственном заводе. Сейчас для его использования совместно с МТС готовится инфраструктура связи, а с декабря 2019 г. проект будет запущен в опытную эксплуатацию. Аналогичные разработки ведутся и для карьерных самосвалов в Кемеровской области в компании «СДС-Уголь».
Сейчас в промышленности все больше применений находится для методов искусственного интеллекта, поэтому «Росстандарт» принял решение сформировать Технический комитет 164, который будет заниматься разработкой стандартов в этой сфере. Его представитель будет присутствовать в международном подкомитете ISO/IEC JTC1 SC42, также занимающемся стандартизацией использования методов искусственного интеллекта, в том числе и в промышленности. На форуме выступил секретарь ТК 164 Андрей Лобунов, который рассказал об особенностях стандартизации механизмов искусственного интеллекта. Сегодня в комитете уже 70 организаций, из них 30 отраслевых. В комитете созданы пять рабочих групп: РГ01 «Основополагающие стандарты», РГ02 «Большие данные», РГ03 «Качество технологий ИИ», РГ04 «Прикладные технологии ИИ» и РГ05 «ИИ в образовании» – структура, которая полностью повторяет рабочие группы международного комитета SC42. Работа этих группах уже началась, и процесс стандартизации использования методов искусственного интеллекта в промышленности стартовал.
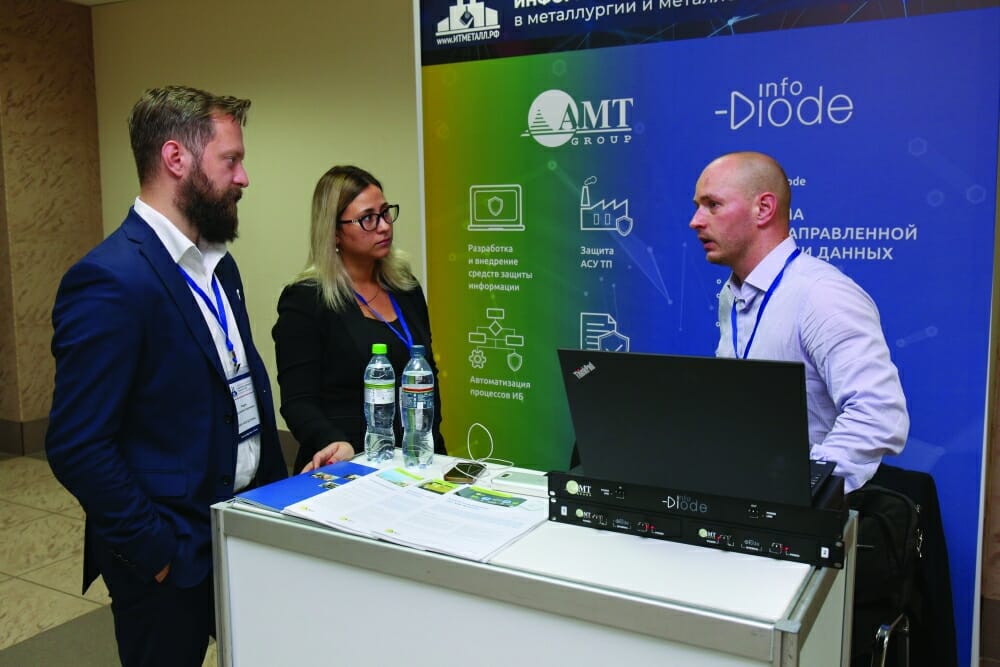
Инновационные разработки рассматривались и на сессии «Инструменты Индустрии 4.0 в металлургии», где обсуждались самые различные аспекты цифровизации промышленных предприятий. Лучшим докладчиком в этой сессии признан Роман Рудин, руководитель направления цифровизации АО «Атомредметзолото», который рассказал о методах оптимизации добычи урана при помощи трехмерного моделирования процедуры выщелачивания. Технология получила наименование «Умный полигон» и была по достоинству оценена слушателями форума. Компания занимается добычей урана методом скважного подземного выщелачивания, предполагающего закачивание в богатые ураном пласты серной кислоты, которая растворяет материал и поднимает его на поверхность. Однако если кислота будет растекаться слишком широко, то эффективность метода существенно снизится. Технология моделирования, разработанная в АО «Атомредметзолото», позволяет регулировать поступление выщелачивающего раствора и откачивание продуктового таким образом, чтобы минимизировать растекание активной жидкости по пласту. По результатам внедрения указанной технологии при отработке месторождения удалось добиться совокупной экономии 170 млн руб.
В сессии были также заслушаны доклады об использовании виртуальной и дополненной реальности на промышленном производстве, беспилотном промышленном транспорте, в организации контроля за технологическими процессами. Алексей Семес, руководитель проекта Объединенной компания РУСАЛ, рассказал о сложностях использования дополненной реальности в промышленности. Оказалось, что в полевых условиях система позиционирования иногда перестает работать адекватно, что приводит к проблемам с использованием приложений. Компания сейчас занимается отработкой технологии обслуживания техники с помощью приложения дополненной реальности в условиях промышленного производства.
Владимир Сидоров, руководитель управления по автоматизации процессов технологических решений ОАО «Северсталь-инфоком», поделился опытом использования виртуальной реальности для тренинга персонала по нештатным ситуациям, созданию маркетинговых VR-роликов и даже организации виртуального соревнования сталеплавов. К сожалению, не для всего оборудования есть трехмерные представления объектов, что приводит к сильному удорожанию проектов в области виртуальной и дополненной реальности – вначале приходится оцифровывать сам объект и строить его трехмерную модель. В результате стоимость проектов составляет от 500 тыс. до нескольких миллионов рублей.
Также в сессии «Индустрия 4.0» Артем Губайдуллин, заместитель руководителя по реализации проектов в области «Индустрии 4.0» ОАО «ММК-МЕТИЗ», рассказал о реализации проекта по внедрению системы удаленного контроля технологических процессов, которые ранее контролировались вручную. На предприятии было внедрено контролирующее оборудование, которое позволило оперативно анализировать показатели качества производимой продукции, повысить технологическую дисциплину и оптимизировать количество задействованного персонала. Система эффективно работает круглые сутки, не снижая качества контроля в ночные часы, как это было при ручном вводе информации.
Защита производства
Важной темой в цифровизации является обеспечение информационной безопасности. Ей была посвящена сессия «Информационная безопасность», в которой ситуацию в области защиты критической инфраструктуры промышленных предприятий раскрыла Елена Торбенко, заместитель начальника Управления ФСТЭК России. Она рассказала о положении дел с категоризацией в отрасли металлургии и горнодобывающей промышленности. В частности, по текущим данным в металлургической промышленности зафиксировано наличие 1588 объектов КИИ, а в горнодобывающей – еще 408. По оценкам докладчика, эти показатели могут вырасти в два-три раза.
Елена Торбенко заявила, что прямого доступа производителя АСУ ТП к его продуктам, установленным на предприятиях критических сфер деятельности, быть не должно. «Мониторинг технологического оборудования необходимо осуществлять через диод данных, а обновление программного обеспечения – через ДМЗ», – пояснила она. Сейчас технологии, которые позволяют организовать подобное взаимодействие с промышленными информационными системами, уже есть, причем их продемонстрировали в рамках выставки форума компании «АМТ-ГРУП» и «АйТи Бастион».
Свой диод данных под торговой маркой InfoDiode представила компания «АМТ-ГРУП». Уже несколько лет он предлагается на российском рынке именно для организации безопасной защиты промышленных сетей – о его особенностях рассказал Андрей Бирюков, руководитель группы защиты АСУ ТП департамента информационной безопасности «АМТ-ГРУП». Аналогичный по назначению продукт под названием «Синоним» продемонстрировала на выставке компания «АйТи Бастион». Строго говоря, он не является классическим диодом данных, но позволяет организовать хорошо контролируемое взаимодействие с промышленной сетью.
Своим опытом создания и управления демилитаризованных зон (ДМЗ) поделился начальник отдела обеспечения безопасности информационных систем ООО «ЕвразХолдинг» Андрей Нуйкин. Он уже несколько лет проводит в своей группе компаний процедуру разделения офисной сети передачи данных и технологических сетей, создавая на производственных площадках ДМЗ. Работа была начата в феврале 2016 г. и позволила защитить технологические сети компании от вируса NotPetya. Сейчас стоит вопрос об оптимизации архитектуры ДМЗ: компания пришла к выводу, что нужно создавать кластерные демилитаризованные зоны, чтобы избежать единой точки отказа, с одной стороны, и не слишком распылять ресурсы на контроль большого числа отдельных ДМЗ – с другой.
Ивана Бадеха, ПАО «ГМК «Норильский никель», представил концепцию сопоставления требований к информационной безопасности, предъявляемых Законом № 187-ФЗ, с уже реализованой на многих предприятиях системой управления рисками. По его словам, безопасность – это не отсутствие угроз, а поддержание непрерывной деятельности предприятия в условиях их наличия. На ГМК была проведена процедура оценки всех типов угроз в соответствии с процедурой категорирования и определены критические для компании процессы. После выполнения всех оценок по классической модели управления рисками обнаружилось, что реализация киберрисков так же опасна для производственной компании, как и нарушение правил промышленной безопасности. «Ущерб от успешной атаки на АСУ ТП сопоставим с потерями от пожара», – отметил Иван Бадеха.
Человеческий фактор
Вопросы человеческого фактора обсуждались на форуме сразу в двух сессиях: «Промышленная безопасность и охрана труда» и «Подготовка кадров для цифровой металлургии». Цифровизация позволяет сделать контроль над персоналом более пристальным и не допускать нарушения им производственной дисциплины, хотя нормативные акты в этом вопросе пока отстают. По словам Алексея Ефимова, заместителя начальника отдела стандартов безопасности труда департамента условий и охраны труда Минтруда России, до сих пор действуют требования по охране труда, разработанные еще в 1929 г. В настоящее время министерство занимается пересмотром и модернизацией устаревших норм и обратилось за помощью к представителям промышленности. В частности, сейчас разрабатываются проекты подзаконных актов по безопасной организации труда в эпоху
цифровизации.
В Министерстве труда и соцзащиты в 2018 г. был проведен эксперимент по переводу в электронную форму документов, связанных с трудовыми отношениями работников и компаний. В нем участвовало 11 крупных компаний – из металлургической отрасли ПАО «Мечел», АО «Северсталь Менеджмент» и ООО «СИБУР». Были выявлены определенные проблемы, связанные с использованием цифровой подписи и электронных форм документов, которые необходимо будет решить. По оценкам, переход на электронные формы документов состоится не раньше 2021 г., но, как пояснил Алексей Ефимов, это не значит, что бумажные документы будут запрещены. Их также можно будет хранить и использовать в своей работе.
Опыт использования специального оборудования для организации охраны труда сотрудников промышленных предприятий обобщила в своем докладе Светлана Водянова, генеральный директор J’son & Partners Consulting. Среди причин, приводящих к наиболее частым травмам сотрудников, – их слабый контроль, неадекватная оценка риска со стороны работника, недостаточное количество тренировок и информирование сотрудников об опасности, некачественные обслуживание и тестирование оборудования и др. Для решения перечисленных проблем вполне применимы современные информационные технологии. В частности, предусматриваются максимальное использование беспилотных аппаратов в зонах повышенной опасности, автоматизация и роботизация опасных производств, строгий контроль доступа к управлению опасными агрегатами и машинами с автоматизированным контролем физического состояния сотрудника, «умные» средства индивидуальной защиты – каски или жилеты. В целом для охраны труда сотрудников предполагается построение интегрированной платформы автоматизированного контроля безопасности работ на промышленном предприятии – Control of Work (CoW), которая позволяет обеспечить интеллектуальное управление рисками в сфере охраны труда сотрудников.
Своим опытом внедрения «умных» устройств для охраны труда сотрудников поделился Всеволод Глущенко, эксперт по развитию новых технологий ОАО «Северсталь-инфоком». Компания «Северсталь» пыталась использовать самые разнообразные методы контроля сотрудников, однако оказалось, что точность современных технологий позиционирования не позволяет определить их местоположение точнее, чем на три метра. Чтобы определить местоположение сотрудника в целях контроля его захода в запретную зону, этого может быть достаточно, а вот для определения и предотвращения столкновения с транспортным средством – нет. Такая задача тоже ставилась перед создателями системы контроля сотрудников на «Северстали». Тем не менее компания тестирует решение с «умными касками» и «умными жилетами» для определения состояния здоровья сотрудников и оценки качества условий их труда. Кроме того, на некоторых предприятиях холдинга тестируются устройства для автоматизации медицинского осмотра сотрудников перед допуском их на опасные производства.
Заключение
В рамках форума также состоялся круглый стол на тему «Цифровизация в металлургии: от фундамента к вершине», партнерами которого стали компании NetApp и Veeam. С приглашенными специалистами обсуждались требования, которые металлургический бизнес предъявляет к ИТ, возможные пути удовлетворения этих требований и ценность накапливаемых в инфраструктуре данных. Подробно о мнениях, обсуждаемых в рамках этого круглого стола, нами подготовлен отдельный материал.
Всего на форуме было заслушано 26 докладов, из которых 19 – от представителей металлургических и металлообрабатывающих предприятий. Форум стал фактически независимой от крупных производителей ИТ-решений площадкой для обсуждения насущных вопросов автоматизации и цифровизации предприятий металлургической и металлообрабатывающей промышленности, где представители отрасли смогли в дружеской атмосфере обменяться опытом использования современных технологий. По каждому докладу проводилось голосование, лидерами стали три докладчика: Ренат Назыров, директор департамента «Сквозная автоматизация» Объединенной компании РУСАЛ, Антон Омигов, менеджер группы «Документооборот» отдела корпоративных разработок ООО «ММК-Информсервис», и Роман Рудин, руководитель направления цифровизации АО «Атомредметзолото». Кроме того, проводился социологический опрос посетителей мероприятия по вопросам цифровизации и автоматизации металлургической и металлообрабатывающей промышленности, результаты которого будут в ближайшее время опубликованы на сайте. В фойе форума работала выставка.
В целом можно отметить, что металлургическая и металлообрабатывающая отрасли России находятся на достаточно высоком уровне автоматизации и даже цифровизации. В ней есть лидеры и догоняющие, причем появляются и новые компании, которые не имеют груза устаревшей техники и ИТ-оборудования. Металлургические компании внедряют только проверенные решения с доказанным экономическим эффектом, потому процесс внедрения длится довольно долго – от пилота к масштабированию на все предприятия территориально распределенных холдингов, однако результат такого внедрения оказывается лучше. Российская металлургическая и металлообрабатывающая отрасли интегрированы в международную систему кооперации, которая требует от предприятий соответствовать высоким международным образцам и лучшим мировым практикам, поэтому компаниям приходится предлагать своим клиентам самые новейшие разработки, основанные на автоматизации и цифровизации собственного производства и логистики.
- ВКонтакте
- Telegram