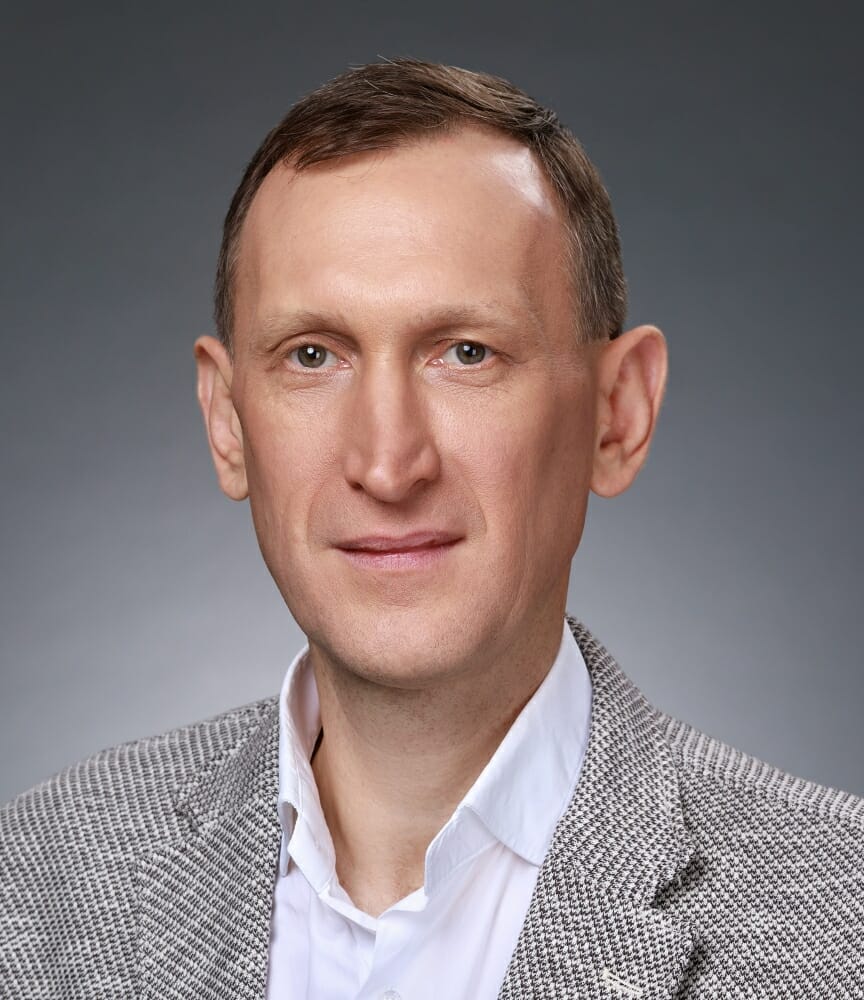
По исследованию Zion Market Research, глобальный рынок предиктивной аналитики в 2016 г. оценивался в 3,49 млрд долл., а в 2022 г. достигнет примерно 10,95 млрд долл. при среднегодовых темпах роста 21% (GAGR). В России оборот предиктивной аналитики в 2018 г. составил 200 млн долл. Промышленные предприятия постепенно переходят к новым стратегиям – проводят интеллектуальный анализ данных, отслеживают фактическое состояние оборудования и обнаруживают его дефекты на ранних этапах. В этом им помогает система предиктивной диагностики.
Интеллектуальная диагностика
В качестве примера рассмотрим систему автоматизированной интеллектуальной диагностики (САИД). Система интересна тем, что для ее запуска не требуется установки каких-либо датчиков, достаточно подключить контроллер к питанию или измерительным цепям. Полученные данные система обрабатывает и формирует прогноз места и времени возникновения неполадок оборудования. На промышленном производстве, где от работоспособности зависят не только выпускаемая продукция, но и возникновение огромных материальные потерь, важно заранее знать о скорой поломке и оперативно ее устранять. В САИД заложен ряд отработанных алгоритмов, которые выполняются в автоматическом режиме без участия оператора. Система диагностирует различные дефекты: нарушения контактных соединений в цепях питания, дефекты ротора и статора, пробои обмоток, проблемы с креплением, дефекты подшипников, поломки приводимого оборудования, а также нарушения технологических процессов, например турбулентность.
Каждая единица оборудования уникальна, поэтому в САИД используется машинное обучение для подстройки под характеристики конкретной машины. Сравнивая текущие показатели с идеальной моделью, система проводит оценку развития дефектов и прогнозирует ожидаемое время работы оборудования до выхода из строя. Вся информация выводится операторам в наглядном виде, а результаты диагностики могут интегрироваться с системами диспетчеризации и управления обслуживанием и ремонтами. Предиктивная диагностика улучшает работу всего производства: исключаются внеплановые остановки, а ремонт осуществляется по фактическому состоянию оборудования.
Основные риски на современном производстве – простои неработоспособного оборудования. По данным концерна Shell за 2015 г., 40% компаний из горнодобывающей и металлургической отраслей за последние три года понесли финансовые потери более чем на 250 тыс. долл. каждое. А нефтеперерабатывающие предприятия теряют до 20 млрд долл в год. Это чистые потери из-за внепланового простоя оборудования и низкого качества продукции. Также при выявлении поломки на производстве многое зависит от человеческого фактора. Мы не можем винить ремонтную службу или сомневаться в ее квалификации, потому что ни один специалист не способен определить поломку на ранней стадии или предугадать ее. Поэтому современному производству нужна точная информационная система, которая в режиме реального времени показывает текущее состояние и вероятность отказа оборудования в ближайшем будущем. Используя системы предиктивной аналитики, компании повышают уровень промышленной безопасности, экономят время на обнаружение поломок и снижают риски сбоев в производственных циклах.
Метод Фурье
САИД обеспечивает косвенные виброконтроль, вибродиагностику и анализ состояния электрической части агрегата. Устанавливать датчики на него не требуется – достаточно подключиться к цепям питания или измерительным трансформаторам. Это хорошо подходит для оборудования, доступ к которому ограничен, например для погружных скважинных насосов и различных систем на морских нефтедобывающих платформах, а также снижает время и стоимость подключения любых других установок.
В процессе диагностики электрическая машина используется как датчик для анализа состояния всей электромеханической системы. Входным сигналом для САИД служат питающее напряжение и ток. Как только мы получаем серии отсчетов и их спектрального преобразования по методу Фурье, формируется выходной сигнал в виде набора гармоник потребляемого электрического тока. Существенная особенность системы – способность просчитать момент, когда дефект разовьется до критического состояния. Другими словами, система прогнозирует, сколько времени проработает оборудование, пока не выйдет из строя. Для специалистов технического обслуживания и ремонта это критически важная информация.
На промышленных объектах возможна установка как автономной системы, которая будет обслуживаться персоналом предприятия, так и облачного сервиса. В случае использования облака КРОК на объекте располагаются приборы и контроллеры для измерения параметров, преобразования отсчетов в спектр и анализа данных. А в облаке размещается аналитический уровень информационной системы. Такой вариант реализации системы привлекает специалистов-диагностиков для анализа и подготовки отчетов о состоянии оборудования – как на периодической, так и на постоянной основе.
Как выбрать правильную стратегию?
При использовании систем предиктивной диагностики на производстве важно выбрать правильную стратегию обслуживания и ремонтов (ТОиР) оборудования. Часто из-за массового внедрения их содержание достигает 20–30% затрат на техобслуживание и ремонты. Не нужно впадать в крайности. Как показывает практика, для начала следует разделить все оборудование на три категории по надежности работы и влиянию на прибыль производства:
- высококритичное оборудование. Влияет на бесперебойную работу производства. Если выйдет из строя, снизится выручка предприятия;
- среднекритичное оборудование. Выход из строя не приведет к падению мощности производства;
- низкокритичное оборудование. Мало влияет на производство.
Также важно понимать состояние оборудования и вероятность выхода из строя. Здесь могут помочь системы предиктивной диагностики. Они определяют состояние и время работы единицы оборудования до его поломки. По этим двум показателям мы видим, что в первую очередь нужно ремонтировать высококритичное оборудование с высокой вероятностью поломки, а после низкокритичное. Такой подход сокращает затраты на ремонты и оперативное перепланирование работ.
Для каждой категории оборудования применяется своя стратегия обслуживания:
- для высококритичного оборудования – стратегия планово-предупредительных ремонтов. Предиктивная диагностика нужна для предупреждения аварий на ранних стадиях. Переход к стратегии «ремонты по состоянию» недопустим;
- для среднекритичного оборудования – стратегия непрерывного мониторинга состояния. Переход к стратегии «ремонты по состоянию» допустим;
- для низкокритичного оборудования – стратегия ремонтов по факту. Однако если из строя выходит зарезервированное оборудование, оно становится критичным и стратегия его обслуживания оперативно пересматривается.
Такой подход минимизирует стоимость жизненного цикла оборудования. А совместное использование предиктивной диагностики с системами минимизации затрат обеспечивает:
- постоянный технико-финансовый аудит хозяйственной деятельности энергетического объекта;
- эффективное и своевременное предупреждение аварий и отказов оборудования;
- управление техническими и экономическими рисками;
- ремонт разных групп оборудования;
- увеличение прибыли предприятия и надежность работы оборудования.
Что было раньше?
До появления предиктивной аналитики и диагностики техническое обслуживание и ремонт планировались заранее. Процессам не хватало гибкости и легкости, чтобы подстроиться под меняющиеся условия. Этот фактор спровоцировал радикальное изменение подхода к автоматизации под лозунгами «Цифровизация» и «Цифровое производство». Цифровизация производственной деятельности меняет как принципы взаимодействия пользователя с системой, так и подходы к проектированию архитектуры. Плюс расширяются функциональные возможности системы управления. Сейчас появляются системы управления жизненным циклом оборудования, которые включают:
- систему управления классификатором и паспортизацией оборудования. Ведение нормативно-справочной информации;
- систему ТОиР со всеми классическими функциями вместе с базой оборудования, планирования ремонтов, управления ремонтом и материально-техническими ресурсами. Кроме того, широкий спектр мобильных решений для минимизации влияния человеческого фактора при проверке оборудования и визуальной оценке его состояния;
- цифровой архив технической документации. В идеале можно ожидать перехода к BIM-технологиям, но пока это целесообразно только для проектируемых и строящихся предприятий;
- предиктивную и интеллектуальную диагностику оборудования;
- системы минимизации стоимости жизненного цикла оборудования на базе индексов экономической надежности и технического состояния. Управление рисками и оценку критичности оборудования (RCM/RCM2);
- системы электронных нарядов-допусков и перевод документооборота в электронный вид. Дополняется автоматизированными медицинскими комплексами и системами позиционирования персонала;
- электронные журналы дефектов, заявок и нарядов для ремонтно-эксплуатационного персонала, которые предназначены для удобного и быстрого ввода информации.
Все эти компоненты позволяют создать систему управления полным циклом жизни оборудования – от разработки до списания, с возможностями предиктивной аналитики остаточного ресурса для организации ремонтов.